1. What is Multiphysics Simulation?

Multiphysics simulation involves the simultaneous simulation of multiple interacting physical systems. In essence, it's a computer-aided design (CAD) tool that allows engineers and scientists to explore how different physical forces—like heat, fluid flow, electromagnetics, and structural mechanics—interact in a system. Rather than analyzing these forces in isolation, multiphysics simulation provides a holistic view, offering deeper insights into complex problems. A few examples of these forces include:
- Thermal effects: How temperature changes affect a material.
- Structural mechanics: How materials deform under stress.
- Fluid dynamics: How liquids or gases move within a system.
- Electromagnetic fields: How electromagnetic forces interact with physical structures.
Check out the video regarding numerical simulations 👇
2. The Benefits of Multiphysics Simulation 🎯
Why should you care about multiphysics simulation? For one, it can reduce time-to-market, optimize product performance, and minimize costs associated with physical prototyping. Here’s a quick look at some of the key benefits:
- Increased accuracy: Multiphysics simulation provides a more comprehensive picture by accounting for the interactions of various physical phenomena.
- Cost savings: Instead of building multiple physical prototypes, you can simulate a variety of scenarios digitally.
- Improved innovation: With deeper insights, companies can push the boundaries of product design.
- Risk mitigation: Early detection of design flaws can save time and resources down the line.
Isn't it amazing how one tool can bring so many benefits?
3. Core Areas of Application 🛠️
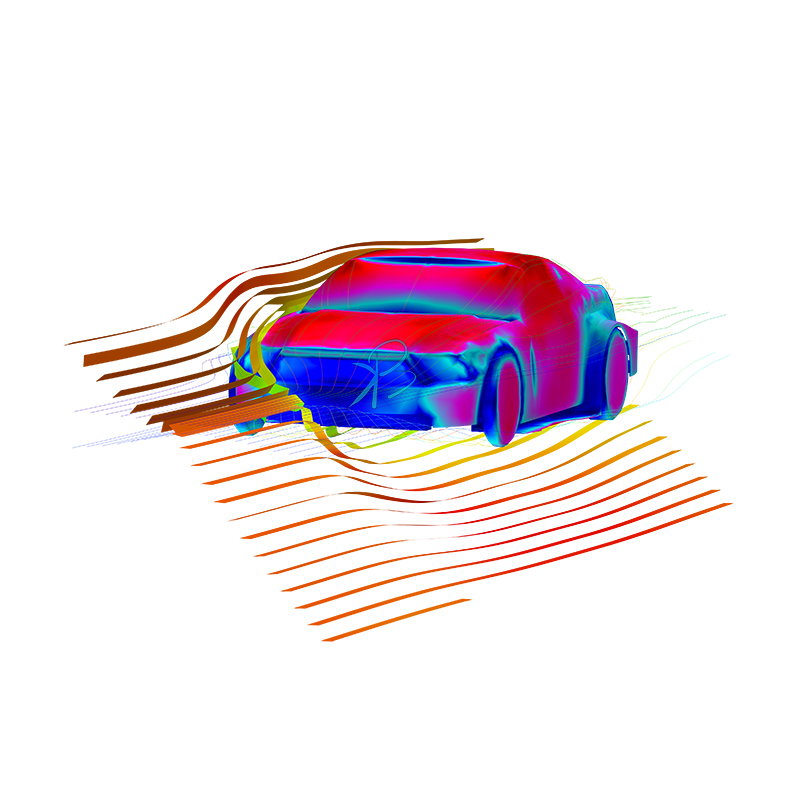
Multiphysics simulation finds itself at the heart of many cutting-edge applications across industries. Let’s look at where it shines the most:
- Aerospace and Defense: Simulating aerodynamics, structural integrity, and thermal effects in aircraft or spacecraft design.
- Automotive: Optimizing engine design by simulating heat flow, fluid dynamics, and structural integrity.
- Biomedical: Understanding fluid flow and heat distribution in medical devices like stents or prosthetics.
- Energy: In renewable energy, it helps optimize wind turbine blades by analyzing aerodynamic forces.
- Electronics: Predicting the effects of heat and electromagnetic fields in electronic components, leading to better designs and durability.
Each of these industries uses multiphysics simulation to streamline processes and create more effective and innovative solutions. Think about how much power that unlocks!
4. How Multiphysics Simulation Works 🛠️
At its core, multiphysics simulation involves complex mathematical models and algorithms. Here's a simple breakdown:
- Model setup: First, the system or product to be analyzed is modeled in a CAD environment.
- Define physics: Physical properties such as heat, fluid flow, and mechanical forces are assigned to different parts of the model.
- Simulation: The interactions between these physical properties are then computed through numerical methods, often using finite element analysis (FEA).
- Analysis: The results show how the system behaves, providing insights for design improvements.
It’s like creating a digital twin of the real-world system and experimenting on it—minus the cost and time of real-world testing.
5. Case Studies: Real-World Applications 🌍
Case Study 1: Tesla's Battery Cooling System Tesla uses multiphysics simulation to design the cooling systems in their electric vehicle batteries. By simulating both thermal and fluid dynamics, they’ve optimized the cooling process to prevent overheating, which is crucial for battery longevity and safety.
Case Study 2: Wind Turbine Optimization Siemens Gamesa Renewable Energy, a global leader in wind turbine technology, relies on multiphysics simulations to fine-tune the aerodynamics of their turbine blades. By simulating airflow, they’ve achieved higher energy efficiency in their designs.
These examples show that even the most complex systems can be optimized with multiphysics simulation, resulting in game-changing advancements.
6. The Future of Multiphysics Simulation 🔮

Looking ahead, the future of multiphysics simulation is nothing short of exciting. Trends such as artificial intelligence (AI) and machine learning (ML) are being integrated into simulation tools, allowing for faster simulations and more accurate predictions.
Cloud-based simulation is also on the rise, providing accessibility to smaller companies that may not have the infrastructure to handle large simulations in-house. This democratization of technology will likely fuel even more innovation across industries.
Imagine the next wave of inventions—fueled by simulations run in the cloud!
7. How to Get Started with Multiphysics Simulation 🚀
Getting started with multiphysics simulation is easier than ever. Here are a few steps to guide you:
- Choose the right software: Tools like COMSOL Multiphysics, Ansys, and Altair are popular choices.
- Invest in training: Many providers offer online tutorials and courses to help you learn the ropes.
- Experiment and iterate: Don’t be afraid to play around with different setups, parameters, and models. The more you practice, the better you’ll get.
While the learning curve may seem steep, the rewards are immense.
8. Frequently Asked Questions ❓
Q: What’s the difference between single-physics and multiphysics simulations? A: Single-physics simulations focus on just one phenomenon, like heat transfer. Multiphysics simulations consider multiple interacting phenomena, offering a more comprehensive understanding of system behavior.
Q: Is multiphysics simulation only for large companies? A: Not at all! While it has historically been used by larger enterprises, cloud-based solutions and more accessible software are opening the doors for small and medium-sized businesses.
Q: Can multiphysics simulation replace physical testing completely? A: While it reduces the need for physical prototypes, it doesn’t eliminate them entirely. Physical testing is still crucial for validating simulation results.
Final Thoughts 💡
Multiphysics simulation is a powerful tool that has revolutionized the way we solve complex engineering problems. Whether you’re in aerospace, automotive, or renewable energy, the benefits are clear: increased accuracy, faster time-to-market, and cost savings. As the technology continues to advance, we can only expect its influence to grow.
For help in modelling in any FEA, FDTD, DFT Simulation / Modelling work, you can contact us (bkacademy.in@gmail.com) or in any platform.
Interested to Learn Engineering modelling? Check our Courses?