1. Introduction: Understanding Numerical Simulation in Manufacturing
Numerical Simulation on Manufacturing - Numerical simulation is increasingly revolutionizing manufacturing processes, providing new ways to model, analyze, and optimize production. By using mathematical models to represent physical phenomena, numerical simulations help manufacturers understand how changes to design, materials, or processes will affect the final product—before committing to expensive physical prototypes.
The question arises: how exactly does this technology shape modern manufacturing processes? 🌐 Let's dive into the specific ways numerical simulation impacts various industries, from automotive to aerospace, and even electronics manufacturing.
Check out the video regarding numerical simulations 👇
2. What Is Numerical Simulation?

Numerical simulation refers to the use of computer algorithms to simulate the physical behavior of objects or systems. In manufacturing, simulations replicate processes like:
- Heat transfer in welding or casting.
- Fluid dynamics in cooling systems.
- Structural analysis in load-bearing materials.
The goal is to predict performance, test innovations, and ensure that manufacturing decisions are cost-effective and optimal.
Popular Simulation Tools:
- Finite Element Analysis (FEA) – Simulates how products respond to stress, heat, and vibration.
- Computational Fluid Dynamics (CFD) – Models the flow of fluids (like liquids and gases) within or around a product.
- Multiphysics Simulations – Simulates multiple interacting physical phenomena, like thermal and mechanical effects combined.
3. Enhancing Product Design Through Simulation 🏗️
One of the most significant impacts of numerical simulation on manufacturing is in product design. Gone are the days of endless physical prototypes! With simulation, engineers can test their designs virtually, resulting in:
- Reduced Prototyping Costs: Instead of creating physical prototypes for every iteration, simulations allow digital testing.
- Speed to Market: Since simulation accelerates the testing phase, products can be refined and launched faster.
- Optimized Designs: Simulations can test extreme conditions, enabling designers to tweak designs for maximum durability and efficiency.
Case Study: Tesla’s Electric Vehicles ⚡
Tesla uses advanced numerical simulations to optimize everything from battery cooling to vehicle aerodynamics. By simulating airflow and structural load, they minimize wind resistance, improve energy efficiency, and ensure vehicle safety—all without excessive physical testing.
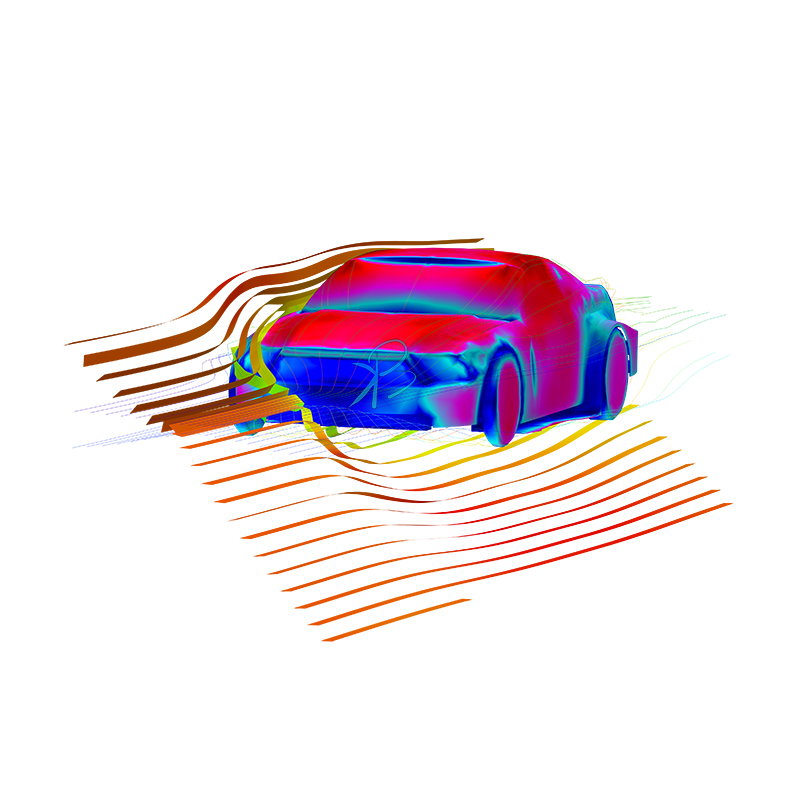
4. Improving Manufacturing Processes 🚀
Numerical simulation doesn’t just help with product design—it’s also transforming the actual manufacturing processes.
4.1 Process Optimization 📊
Through simulation, manufacturers can model and analyze the production line, identifying bottlenecks and inefficiencies. For example, in additive manufacturing (3D printing), simulations can predict material behavior to optimize layer thickness, printing speed, and temperature.
4.2 Reducing Waste 🛠️
Simulations also predict how materials will behave during processes like metal forming or injection molding, ensuring the most efficient use of raw materials. This minimizes errors and reduces scrap rates, contributing to more sustainable manufacturing practices.
4.3 Enhanced Quality Control 🏅
By simulating production outcomes, manufacturers can spot potential defects before they occur. For instance, a casting simulation may reveal where voids or weak spots could develop in a metal part, allowing adjustments before actual production begins.
5. Numerical Simulation in Specific Manufacturing Sectors 🏭
5.1 Automotive Industry 🚗
Automakers extensively use numerical simulations for crash testing, aerodynamics, and even engine optimization. Simulations of car crashes help manufacturers meet safety regulations without the need to destroy multiple prototypes, saving both time and money.
5.2 Aerospace Industry ✈️
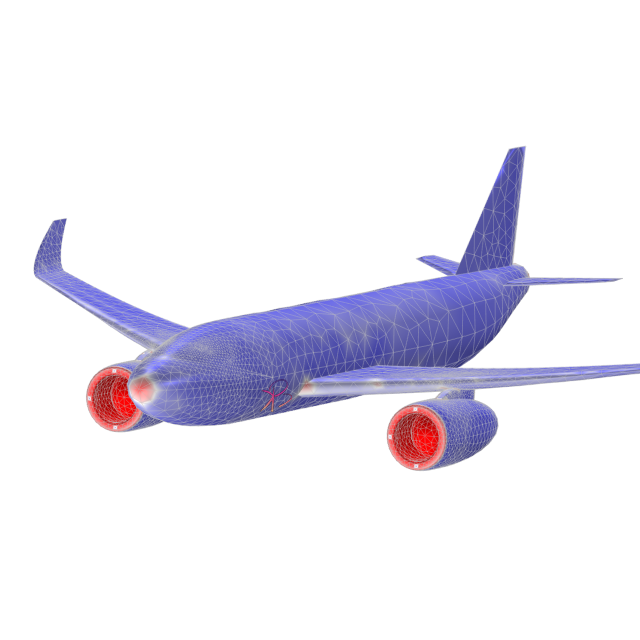
For the aerospace industry, numerical simulations are critical in material testing and fatigue analysis. Aerospace components face extreme conditions (temperature, pressure, and stress), and simulations allow for precise prediction of how these parts will hold up over time, reducing the risk of catastrophic failure.
5.3 Electronics Manufacturing 🔌
In electronics, simulations are used for thermal management and signal integrity analysis. With components packed tightly together, manufacturers use simulations to predict heat generation and distribution, ensuring optimal cooling and performance.
6. Challenges and Limitations ⚠️
While numerical simulation offers significant advantages, it does come with certain limitations:
- Accuracy of Models: Simulations are only as good as the models used. If the physical phenomena are not well understood, the results might be inaccurate.
- Computational Resources: High-fidelity simulations require vast amounts of computing power, especially for complex systems involving multiple interacting phenomena.
- Cost of Implementation: Setting up simulation software and training staff can be expensive, making it less accessible to smaller manufacturers.
7. The Future of Numerical Simulation in Manufacturing 🔮

As computing power increases, the role of numerical simulation in manufacturing will only grow. The adoption of Artificial Intelligence (AI) and Machine Learning (ML) within simulations is likely to enhance predictive capabilities. Imagine simulations that not only model current designs but also predict future problems based on learning from past data! 😲
Additionally, real-time simulations are becoming a reality, enabling manufacturers to adjust processes dynamically during production—a concept known as digital twins.
8. Conclusion: A Game-Changer for Manufacturing 🌟
Numerical simulation has transformed the way products are designed, tested, and manufactured. From reducing costs and waste to speeding up time-to-market, its impact is undeniable. While challenges remain, the continued advancements in simulation technologies, powered by AI and machine learning, promise a future where virtual and real-world manufacturing are seamlessly integrated.
So, whether you’re an engineer, manufacturer, or just someone fascinated by how things are made, the future of manufacturing is undoubtedly shaped by the power of simulation!
For help in modelling in any FEA, FDTD, DFT Simulation / Modelling work, you can contact us (bkacademy.in@gmail.com) or in any platform.
Interested to Learn Engineering modelling? Check our Courses?